Facilities
Granular Shear Cell (GSC)
This granular shear cell helps to study the flowing and shearing behavior of grains between relatively moving surfaces. This cell allows one to study the grain flow velocity, solid fraction, granular temperature (i.e., velocity fluctuation), energy dissipation during flow, and slip velocities.
To impose shear on test grains within the GSC, the inner rotating wheel has can be given a prescribed roughness. The GSC has an aluminum frame with a transparent body so that the dynamic behavior of the grain flow can be observed using high-speed photography where the particle position and velocimetry data are known as a function of time. The moving wheel is attached to a 1/16 HP motor capable of achieving rotational speeds of 53–280 rpm, which corresponds to a linear velocity of 0.55–2.89 m/ s. |
|
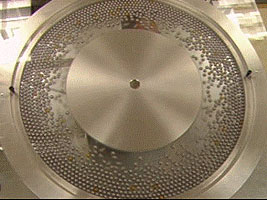
|
Photron FASTCAM SA4 (High-speed camera)
High performance CMOS sensor technology providing 3,600 frames per second (fps) operation at 1024 x 1024 pixel resolution and frame rates up to an astonishing 500,000 fps at reduced resolution.
To complement the existing range of Photron high-performance high-speed imaging products, the FASTCAM SA4 delivers a fully featured system including mega-pixel resolution, high light sensitivity, high dynamic range and low noise at an attractive price level. For demanding applications that do not require the highest frame rates but where all other aspects of system specification are important the FASTCAM SA4 is the correct choice.
Applications include multiphase flows, tribology debris generation, fluid dynamics, biomechanics, material test, airbag development and test, microscopy and granular flow. The high-speed CCD camera is used to capture images of granular flow data such as solid fraction, particle velocity, and slip. |
|
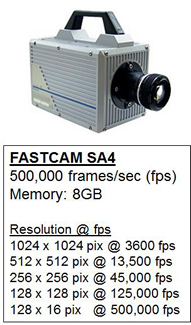 |
Particle attrition tester (PAT)
A particle attrition tester (PAT) allows test particles to be sheared in sliding contacts
under load and high-shear to induce attrition or particle wear for the test materials. The
PAT works similar to a journal bearing in that the center shearing wheel imposes a load
on to the grain materials as they are sheared. The varying eccentricity between the inner rotating wheel and the outer stationary ring depends on the dynamic state of the granular materials in the interface. Thus, grains are entrained into a high-load, high-shear zone which causes high contact stresses within the grain flow, which leads to particle fracture and attrition. The PAT allows different loads and shear rates to be applied to the granular material. Following the PAT tests, particles are characterized for surface and bulk damage, and attrition levels are measured. |
|
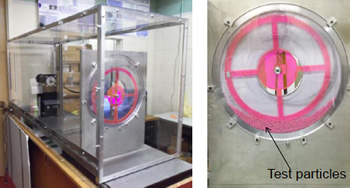 |
Coefficient of restitution (COR) tester
Single granular particles can be dropped from various heights and COR based on height
or velocity is computed. The apparatus is used to measure the coefficient of restitution
(COR) between colliding materials. The figure shows a photograph (a) and an annotated
diagram (b) of the
experimental apparatus.
In the right figure b, the
labeled components (A – G) are defined as a
Plexiglas casing (G), air hose/pump (E/F), base plate and plate holder (A and B), sphere being tested (D), and device for holding the sphere being dropped (C). The casing (G) provides
holes which fix the holding device (C) in place at different heights. The air hose/pump (E/F) provides a suction force to the holding apparatus (C), which is turned on to hold a sphere (D) in place, and then switched off to allow the sphere to drop from rest. This type of setup minimizes spin during the drop. The base plate (A) is secured in place at the bottom of the apparatus by a holder (B). This plate is what the test particle or sphere collides with during each trial. Consequently, the COR can be obtained between the sphere and plate materials. |
|
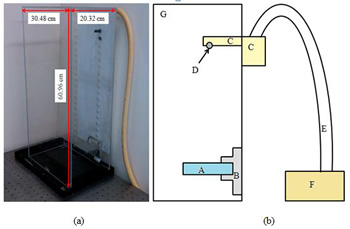 |
Advanced multi-scale load & speed tribomter
The Bruker UMT-3 Tribometer is specifically designed for comprehensive macro-mechanical tests of metal and ceramic materials, lubricants/fluids, rocks, and particle matrices with a load range of 0.1N to 1kN. It performs automated synchronized control of several specimen motions with linear speeds from 0.1μm/s to 30m/s, and angular speeds ranging from 0.001 to 7,000rpm. All motions are independently programmable (for custom wear tracks), and automatic coefficient of friction versus load/velocity curves are generated (tribological finger print).
The world’s most advanced tribometer is used for measuring the friction, attrition/wear, thermal, and electrical contact behavior of particles and materials in sliding contact.
The UMT-3 has or is upgradeable to include a variety of drive modules:
- Lower linear fast reciprocation with upper linear motion
- Lower high-precision linear with upper linear motion
- Lower rotation (vertical axis) with upper linear or rotary motion
- Lower rotation (horizontal axis) with upper linear or rotary motion
Our UMT-3 has or is upgradable with chambers for vacuum, humidity, and gases, and can load up to 2,000N with temperatures up to 1,000°C. Static or dynamic lubrication can be tested using computer controlled pumps. The system monitors and records in situ acoustic emission, electrical data, friction, wear, down force, temperature, humidity, etc., and is ISO, ASTM and DIN compliant.
|
A Hysitron "TriboIndenter" Nanoindenter
The Hysitron “Triboindenter” Nanoindenter performs mechanical nano-characterization and measurements of 3D surface topography of particles and surfaces using scanning probe measurement (SPM) capabilities. It can be upgraded to include additional heating/cooling and to measure dynamic viscoelastic responses.
The TriboIndenter is a complete automated nanomechanical test system, ideal for measuring the hardness and elastic modulus of thin films and coatings, as well. It provides quantitative nanomechanical testing capabilities with the convenience of modern automation. It revolutionizes the sub-micron scale testing arena with real-time data collection and nanometer resolution in situ SPM imaging.
Hysitron's patented transducer technology offers 2-dimensional nanoscale force and displacement measurements, providing quantitative testing based on controlled nanoindentation of surfaces. Automated precision testing, staging and sample positioning allows maximum throughput of samples.
Current or upgradeable features:
- Hysitron’s patented capacitive transducer provides industry-leading sensitivity and stability
- Automated testing for high throughput and statistical sampling of materials
- In situ imaging provides nanometer precision positioning and the convenience of SPM topography
- Acoustic and thermal enclosure, along with stable transducer design, minimizes set-up and stabilization time
- Top-down optics for viewing and selection of testing sites
- Active vibration isolation table
- Sub-micron resolution staging for sample positioning
- Numerous add-ons that allow the widest array of testing capabilities on the market
- Active vibration dampening systems ensure low noise and uncompromised sensitivity
|
Zygo NewView 7300 Optical Profilometer
The NewView™ 7300 white light interferometers is for characterizing and
quantifying surface roughness, step
heights, critical dimensions, and other
topographical features with excellent
precision and accuracy. All measurements
are nondestructive, fast, and require no
sample preparation. Profile heights
ranging from < 1 nm up to 20000 μm at
high speeds, independent of surface
texture, magnification, or feature height.
Using ZYGO's patented scanning white
light interferometry (SWLI) technology,
the NewView™ 7000 series 3D optical
surface profilers easily measure a wide range of surfaces, including smooth,
rough, flat, sloped, and stepped surfaces. |
|
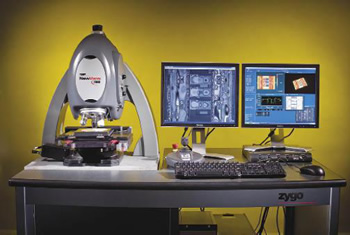 |
Park XE-70 Atomic Force Microscope
The XE-70 incorporates a flexure-based decoupled xyz
motion stage with 100 um measurement range. The
flexure scanner is highly accurate with an out-of-plane
movement 2 nm over the 100 um scan range. The AFM can be operated in an environmental chamber with:
Standard Imaging
• Basic Contact AFM and DFM
• Lateral Force Microscopy (LFM)
• True Non-Contact AFM
Chemical Properties
• Chemical Force Microscopy with Tip
• Electrochemical Microscopy
Dielectric/Piezoelectric Properties
• Electric Force Microscopy (EFM)
• Dynamic Contact EFM (DC-EFM)
Electrical Properties
• Conductive AFM (Ultra-Low & Variable Current)
• Scanning Capacitance Microscopy (SCM)
In-liquid Imaging
• Ion Conductance Microscopy (ICM)
Magnetic Properties
• Magnetic Force Microscopy (MFM)
• Tunable MFM
Mechanical Properties (Force Modulation Microscopy; Nanoindentation) |
|
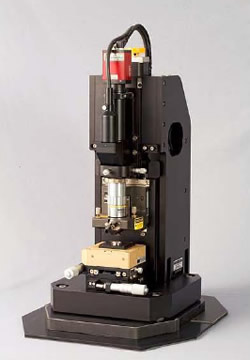 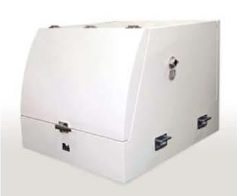 |
Chemical mechanical polishing (CMP) R&D test machine (G&P POLI-300)
Chemical mechanical polishing (CMP) is a complex process in which a wafer surface is planarized by mounting it on a rotating chuck and pressing it against a rotating pad that is flooded with slurry consisting of a fluid and abrasive nanoparticles.
The GNP POLI-300 is designed for R&D CMP process development applications such as integrated circuits, MEMS, as well as CMP parametric study.
Specifications:
- Head, Table: 30~200 rpm, Rotational Motion, Head Oscillation (±12mm)
- Size: 960W * 1000D * 1950H mm
- Table Size: Φ 406 mm (16 inch)
- Pressing Method: Variable Air Pressure Electronic Controller
- Carrier Type: 70~700 g/cm2 (1 psi ~ 10 psi) for 4" Wafer
- Membrane Type: 50~500 g/cm2 (0.7psi ~ 7 psi)
- Process: Automatic Sequence, Dry-in / Wet-out
Options:
- Conditioning: Oscillating Head Type or Swing Arm Type
- Double Head System
- Friction Force & Temperature Monitoring System
Applications:
- Workpiece: Max 6 inch wafer, MEMS Structure, Coupon Wafer
- CMP Process: Si CMP, Oxide CMP (BPSG, TEOS, SC), Metal CMP (W, Cu), STI. |
|
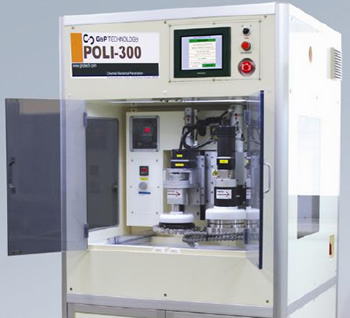 |
Pad-on-disk tribometer with transfer film deposition / Rock Cutting modules
The figure illustrates the High speed PFTL Tribometer Setup, currently in the rock cutting module, but with annotations for the transfer film deposition module as well. The machine can be used to collect in situ data for friction, lubrication, and wear of two sliding contacts simultaneously. The main drive consists of a driver pulley connected via a v-belt to a driven pulley that carries the test spindle. The test spindle is supported at its end by two angular contact bearings and a cylindrical roller bearing.
A variable frequency drive (VFD) controls the 3-phase 1750 rpm, 5-hp motor. Rotational speeds up to 5000rpm can be reached. To measure the transfer film rate as well as in situ depth of cut, a linear voltage differential transducer (LVDT) is used. |
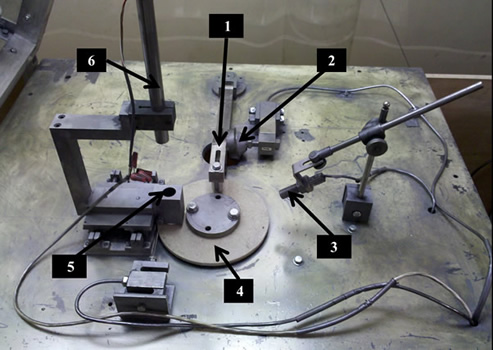 |
1. Variable Radius Slider Pad / Cutter Assembly
2. Load Cell: (in situ Friction Force) Res: 0.44N
3. Tachometer (in situ Velocity) Res: 5rpm
4. Metal/Polymer/Rock Disk (Rotated during Testing)
5. Solid Lubricant Pellet/Trench Tracer Holder (in situ Transfer Film Deposition / Depth of Cut)
6. LVDT (in situ Wear / Depth of Cut) Res: 12/7 µm |
The PFTL leverages full access to other CMU facilities, such as:
- Electron Microscopy Facility
- Nanofabrication Facility
- Microelectromechanical Systems Laboratory
- MSE Material Characterization Facilities
The CMU Material Science & Engineering (MSE) department has an extensive material characterization facility available to faculty for structural characterization, materials processing, or mechanical/physical property / performance determination. For example, the core of the facility is the J. Earl and Mary Roberts (JEMR) Microstructural Characterization Suite. This special facility is open to all research groups within the university for structural and microstructural characterization using electron, x-ray, and scanning probe methods.
|